Comprehensive Guide: What is Porosity in Welding and Exactly How to avoid It
Comprehensive Guide: What is Porosity in Welding and Exactly How to avoid It
Blog Article
The Science Behind Porosity: A Comprehensive Guide for Welders and Fabricators
Comprehending the detailed mechanisms behind porosity in welding is important for welders and producers making every effort for impressive workmanship. As metalworkers explore the depths of this phenomenon, they uncover a world governed by different aspects that affect the formation of these small spaces within welds. From the composition of the base materials to the ins and outs of the welding procedure itself, a plethora of variables conspire to either aggravate or relieve the visibility of porosity. In this detailed overview, we will certainly unwind the science behind porosity, exploring its effects on weld quality and unveiling progressed strategies for its control. Join us on this journey through the microcosm of welding imperfections, where precision fulfills understanding in the quest of flawless welds.
Understanding Porosity in Welding
FIRST SENTENCE:
Evaluation of porosity in welding discloses important understandings into the integrity and quality of the weld joint. Porosity, identified by the presence of cavities or gaps within the weld steel, is an usual concern in welding procedures. These spaces, if not effectively dealt with, can endanger the architectural integrity and mechanical homes of the weld, bring about prospective failings in the finished product.

To identify and evaluate porosity, non-destructive screening techniques such as ultrasonic testing or X-ray inspection are typically utilized. These methods allow for the identification of inner flaws without jeopardizing the stability of the weld. By evaluating the size, form, and circulation of porosity within a weld, welders can make educated decisions to boost their welding procedures and accomplish sounder weld joints.
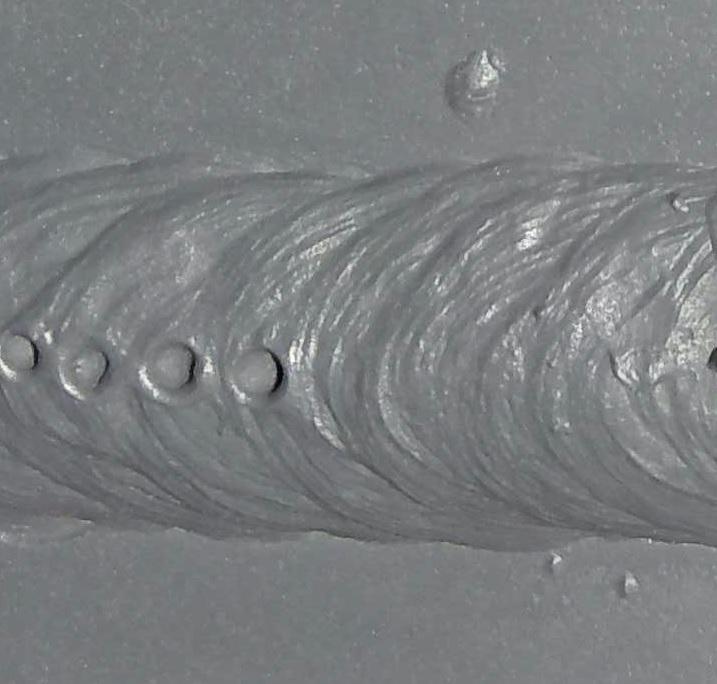
Factors Affecting Porosity Development
The event of porosity in welding is affected by a myriad of factors, ranging from gas shielding effectiveness to the complexities of welding specification settings. Welding parameters, including voltage, present, take a trip rate, and electrode type, likewise impact porosity formation. The welding technique used, such as gas steel arc welding (GMAW) or protected metal arc welding (SMAW), can influence porosity formation due to variants in warm distribution and gas coverage - What is Porosity.
Effects of Porosity on Weld Top Quality
Porosity development significantly endangers the structural stability and mechanical buildings of bonded joints. When porosity exists in a weld, it develops voids or tooth cavities within the product, decreasing the total toughness of the joint. These gaps act as tension focus factors, making the weld extra at risk to cracking and failing under load. The visibility of porosity additionally compromises the weld's resistance to corrosion, as the trapped air or gases within the spaces can react with the surrounding home environment, bring about destruction in time. In addition, porosity can prevent the weld's ability to withstand stress or influence, further threatening the general high quality and reliability of the welded framework. In essential applications such as aerospace, automotive, or architectural buildings, where security and longevity are extremely important, the harmful impacts of porosity on weld top quality can have serious consequences, emphasizing the relevance of minimizing porosity via correct welding strategies and procedures.
Methods to Minimize Porosity
To boost the high quality of welded joints and make sure architectural honesty, welders and producers employ certain techniques focused on reducing the development of gaps and cavities within the product during the welding procedure. One efficient method to minimize porosity is to make certain correct material prep work. This includes comprehensive cleaning of the base metal to eliminate any go kind of impurities such as oil, oil, or dampness that could add to porosity formation. In addition, utilizing the proper welding parameters, such as the correct voltage, present, and take a trip speed, is critical in avoiding porosity. Preserving a constant arc length and angle during welding also helps reduce the probability of porosity.

Using the appropriate welding strategy, such as back-stepping or utilizing a weaving motion, can additionally assist disperse warm uniformly and lower the possibilities of porosity formation. By implementing these strategies, welders can efficiently minimize porosity and generate top notch welded joints.

Advanced Solutions for Porosity Control
Applying innovative technologies and innovative techniques plays a crucial duty in attaining superior control over porosity in welding procedures. One innovative remedy is using advanced gas combinations. Protecting gases like helium or a mixture of argon and hydrogen can assist decrease porosity by providing far better arc stability and enhanced gas insurance coverage. Furthermore, employing sophisticated welding methods such as pulsed MIG welding or customized ambience welding can likewise aid minimize porosity issues.
Another advanced service involves making use of advanced welding devices. For instance, using devices with integrated features like waveform control and sophisticated power sources can boost weld quality and decrease porosity dangers. Additionally, the application of automated welding systems with exact control over criteria can dramatically minimize porosity defects.
Additionally, integrating innovative tracking and assessment innovations such as real-time X-ray imaging or automated ultrasonic testing can aid in discovering porosity early in the welding process, permitting prompt rehabilitative actions. On the whole, incorporating these sophisticated services can significantly improve porosity control and boost the total top quality of welded components.
Verdict
In verdict, comprehending the scientific research behind porosity in welding is necessary for welders and fabricators to create top quality welds - What is Porosity. Advanced services for porosity control can additionally enhance the welding procedure and find out ensure a strong and reliable weld.
Report this page